Cell Block - Carroll, Cell 219 |
An account of the experiences I've witnessed during my year abroad studying in the USA, at Central Connecticut State University
Introduction
Hi, my name is Phil North. I am currently a student at UCLan in Preston studying Creative Writing and Journalism and have been given the opportunity to study my second year at Central Connecticut State University. Here is where you will be able to find out about my experiences, opinions and just how well I'm adjusting to the US way of life.
Wednesday, 28 November 2012
Cell Block - Carroll, Cell Number 219
Labels:
Barbers,
Bored,
CCSU,
Cell Mates,
Clippers,
Connecticut,
Haircut,
Travel,
UCLan,
USA
Thanksgiving
Happy
Thanksgiving from America! With five days off University to celebrate my first
Thanksgiving, Evan invited me to his house to join in the festivities.
On
the Wednesday we travelled east to Columbia, which is next to Lebanon, which is
next to Scotland, you'd have thought the Americans would have thought up some original names for their towns. I was introduced to his Mother - Eva, brother – Nathan, their
3 cats, one of which has seven toes on each foot, his two dogs, the sheep, and
a horse that they adopted to save it from being put down. The poor guy is 40+
and loves to just stand in the sun eating grass, despite having no teeth left.
Strongbow improves steadiness |
![]() |
Born hunter |
After
being told when and where to meet for Thanksgiving, we moved on to his Dad -
Michael and Step-mum – Chris’ house in Lebanon and was introduced to them.
Unfortunately there were no animals to pamper, but I did meet his half-brother,
James, who has the joy of being bullied by his two older brothers. The day was
filled out shooting targets in the back yard with a pellet rifle and beer. Despite
only ever holding a paintball gun, I managed to hit every target.
Thursday,
the day of Thanksgiving, Evan and I awoke to the Macy's Thanksgiving Parade that was being held in New York on the T.V. America makes me laugh. The camera was stationary on the section outside of Macy's and the commentators commented on whatever float was in that section. The funny bit is how each float, and whatever popstar that was singing/miming on it, was advertising something. Now I'm not naive enough to think that there would be another reason, but they weren't even being subtle about it. The commentators would tell us about an upcoming album, DVD release dates, tour dates etc for every float. In addition to this there are adverts every 5 minutes advertising what we had just seen on the floats in case we went to the toilet and missed it.
Later on we made our way to Evan’s Grandparent’s house. A
little confusing but as Eva grew up, her Parents and Grandparents all lived under
one roof. All being Latvian the Grandparents were known as Vetsamom and
Vetsapop, and the Parents (Evan’s Grandparents) were known as Oma and Opa,
which is German as they spent time there growing up. Despite both living in Latvia and spending part of their lives in Germany, they didn't actually meet until they both got to America. Having spent time working in England, Opa told me how he worked for a company in Sheffield that did work for the Government. He found it amusing how laid back the workers were, having a brew in the morning before they started then going to the pub early for dinner and coming back late and having more brews; especially as it was Government work. As we sat Oma presented us with a lovely Turkey whilst Opa presented us with a cupboard full of spirits. Evan was selected to cut the turkey whilst Opa told me of his time working in Sheffield, laughing at our laid back nature and love of the pub.
Evan - Master Carver |
Oma - Master Chef |
On Saturday, Evan and I woke to watch Toy Story 3, then it was back to Oma and Opa’s to bake Latvian cookies. With Oma and Eva in control of the dough and oven, Opa, Evan, Nathan, and I were in charge of shape cutting. If Opa ever offers to get you a vodka coke, be prepared for a proper measure. Basically vodka with some colouring; he’s a good man. With Christmas music on in the background, beers at hand, and Opa trying to convince us that he wore the trousers in the house, we were in for a fun afternoon. For tea we had Chinese takeaway, now this is when Oma proved her role as trouser wearer in the house. As the list was passed around, Opa asked if anyone was having the Peking Duck? Before anyone could answer, Oma told him that he wasn't getting any, she would cook duck another day. Now according to Evan, Opa always wants to have Peking Duck but is never allowed as Oma says that it will take too long. The poor man just wants some duck. Then again the 2 have been married for 60 odd years, just goes to prove that a happy wife is the key to a successful marriage. Happy wife - happy home.
Thanksgiving Meal |
![]() |
The Master & The Apprentice |
With
Evan and me returning to University the next day I said my goodbyes to Oma and
Opa. I was told that I am welcome back any time, and I will always have my very
own Oma and Opa here in America.
New Mexico Free-Kick |
For
our final day, we had some left over Thanksgiving meal for dinner at Michael
and Chris’ (3rd of the break) then went on to watch the University of Connecticut (Uconn) play New
Mexico University at football. With 4300 on the terraces it was packed, which
in hindsight was good as the temperature was just above freezing, and the cold
wind made it feel well below. The game wasn’t the best and the supporters that surrounded us were very annoying with their opinions that screamed out that they had never played the game.
After a Uconn midfielder jibbed out on a header in his own half, New Mexico broke and scored after the goalkeeper parried out. New Mexico dominated the game, finding their players in acres of space due to Uconn's zonal marking, something I've never agreed with. Unfortunately they couldn't capitalise on this dominance. In the second half Uconn equalised after the New Mexico goalkeeper stuck to his line. The first cross should have been a simple punch, the second was trickier but still should have been claimed and then the ball was headed in at close range. As the game neared the final whistle, New Mexico won a free kick that the attacking player controlled beautifully as the ball came in leaving the Uconn players wrong footed. Unfortunately however, he failed to tap into an open net. With the scores level at half time, the game went into golden goal. but Uconn managed
daylight robbery to win the game by golden goal after a defensive mistake. The full back dilly-dallied on the ball and was caught by the Uconn striker who squared it to his strike partner who finished well to send them into the quarter finals.
All in all, Thanksgiving was a huge success and I would like to thank Evan, Eva, Michael, Chris, Opa & Oma for their wonderful hospitality. I've never felt more welcome.
Labels:
CCSU,
Clitheroe,
Columbia,
Connecticut,
Football,
Latvia,
Macy's Parade,
New Mexico,
Shooting,
Soccer,
Stongbow,
Thanksgiving,
Toy Story,
Travel,
Turkey,
UCLan,
Uconn,
USA
Sunday, 18 November 2012
Connecticut Whale Vs Portland Pirates
At the beginning of the year, Erik and I were walking through the Student Centre when a local lad noticed that I was wearing my Rovers shirt. Coming over to us he asked if that was my alliance. Once I realised that he was asking if that's who I supported he told me that he supports Newcastle United, for the sole reason that he likes to drink Newcastle Brown Ale - good a reason as any I suppose.
It turns out that this guy, Phil, is a Geography major and big sports fan. Doing Geography he was interested in things back in Sweden and England and offered to take us to an Ice Hockey game as that is his main sport. The problem at the moment is that the NHL is currently in a lockout due to disagreements with money and contracts. USA Today can probably explain things better than I:

STORY HIGHLIGHTS
- The NHL and its locked out players will resume negotiating Monday to save the season.
- No positions have changed but the sides agree talking is better than nothing.
- More cancellations can be expected within a week if a new deal is not struck.
Conversations that restarted Friday between NHL deputy commissioner Bill Daly and NHLPA special counsel Steve Fehr produced enough positive movement Saturday to set up another face-to-face meeting that the sides hope will lead to an agreement to save the hockey season.
NHL Commissioner Gary Bettman suggested to union executive director Donald Fehr on Thursday the sides take two weeks off from negotiations. The union maintained its desire to keep talking, and now bargaining is back on.
Owners and players met for several consecutive days last week in New York, but made little progress. Negotiations ended in an angry exchange last Friday, but bargaining resumed two days later, only to break off again in just over an hour.
Staying apart never appeared to be a good option, and the NHL now seems to agree.
All games through Nov. 30 have dropped from the schedule. More cancellations are likely within a week. The Winter Classic has been wiped out, the All-Star game is the next big event in jeopardy and the whole season could be lost, too, if a deal can't be hammered out.
The players have stuck to their position that negotiations are the only way to work out differences, and that they are willing to meet any time suggested by the NHL.
The NHL contends the union has submitted the same proposal multiple times without moving in the league's direction. The union says it has agreed to come down from receiving 57% of hockey-related revenues to a 50-50 split. The league wants that to go into effect in the first year of the agreement, while the union wants to get there gradually.
Seven years ago, after the entire 2004-05 season was lost to a lockout, the players' association accepted a salary-cap system for the first time. The union feels it shouldn't have to bear the brunt of the concessions now after league revenues reached a record high of more than $3 billion last season.
This 63-day lockout has claimed 327 regular-season games, and hope of a new deal and the start of the already-shortened season - likely of 68 games per team - on Dec. 1 has started to wane.
It is more than just finances preventing a deal. The disagreements over player contract terms have emerged as just as big an impasse.
The NHL wants to limit contracts to five years, make rules to prohibit back-diving contracts the league feels circumvent the salary cap, keep players ineligible for unrestricted free agency until they are 28 or have eight years of professional service time, cut entry-level deals to two years and make salary arbitration after five years.
Once those issues are settled, the sides will then have to figure out who will cover the financial damage the lockout will ultimately do to this season.
Players missed their third pay day of the season Thursday, and the clock is ticking toward more losses. The 2004-05 season was canceled in February. A lockout in 1995 ended in January, leading to a 48-game schedule.
![]()
|
Shoots: L
Height: 5-10
Weight: 204
2011-12 Team(s): NY Islanders (NHL) & Bridgeport (AHL)
Hometown: Guelph, Ont.
2011-12 Team(s): NY Islanders (NHL) & Bridgeport (AHL)
Hometown: Guelph, Ont.
Now this guy was in both fights and he wasn't even the player that was hit. At 5ft10in he may have a minor case of short man syndrome but whenever his team-mates get roughed up, he sprints across the ice and drops the gloves. Every cloud though, 2 fights - 2 Connecticut wins! I wonder if FIFA would ever consider allowing refereed fights in football?
The only video I could find, it seems to cut the end off though.
Labels:
AHL,
CCSU,
Clitheroe,
Connecticut,
Connecticut Whale,
Ice Hockey,
Michael Haley,
NHL,
Portland Pirates,
Travel,
UCLan,
USA
Thursday, 15 November 2012
Landlords Are Not Slumlords
![]() |
Media Section Of The Council Meeting |
Landlords Are Not
Slumlords
Townspeople of New
Britain flooded to the town council meeting on Wednesday 14th
November to protest against a new license to Landlords in the area, and a fee
for multiple police responses throughout the year.
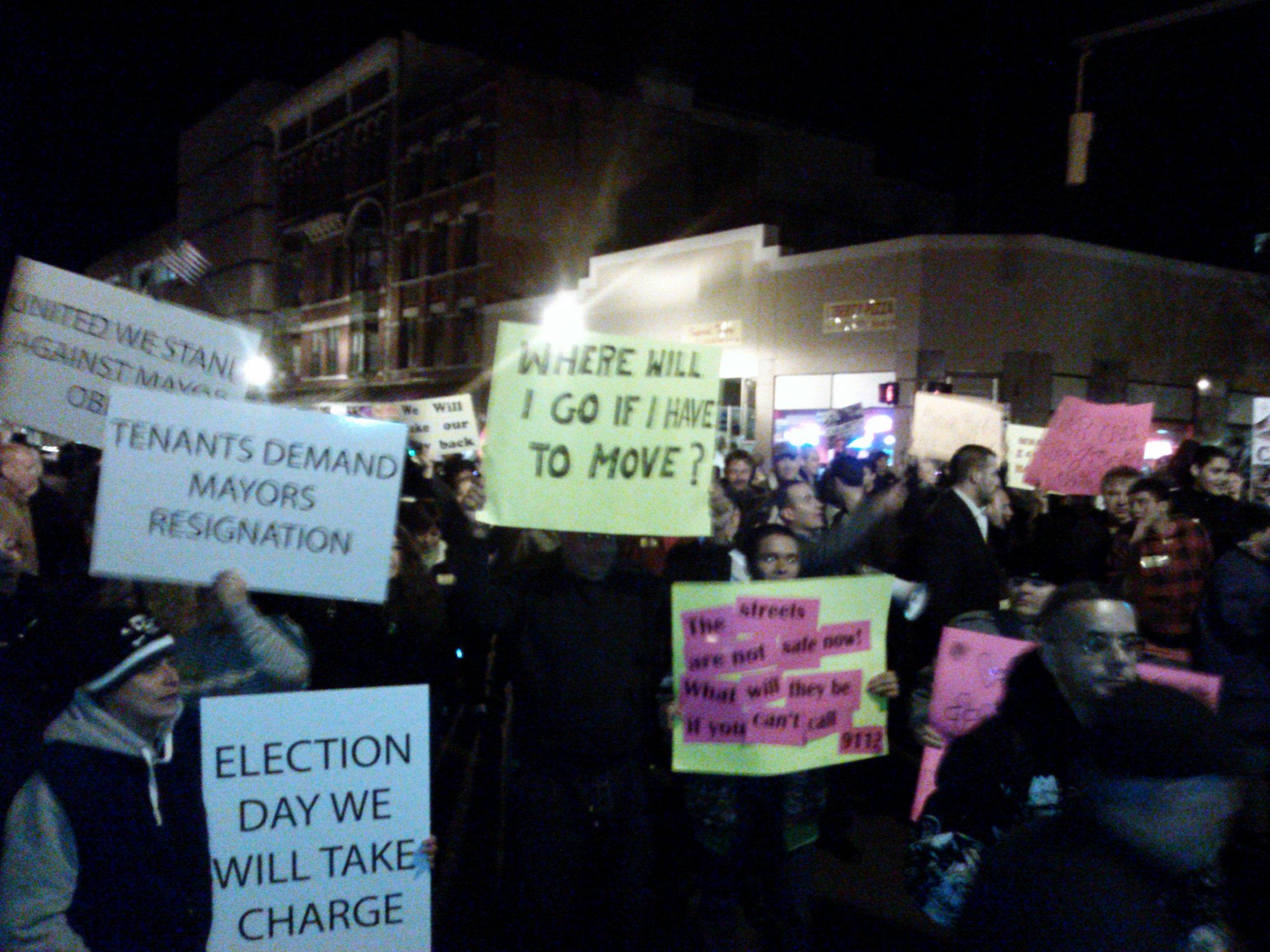
The owner of family
business Atamo’s was unhappy at the increase in taxes, “I don’t rent out any
space, but if this is the way things are heading, surly it won’t be long until
they put the taxes up on business properties.”
Local business owners
will find that these new laws will freeze economic development in the city and
business will suffer.
The Chamber room within
the town hall was full to the brim, with people stood around the periphery and
even more held in the corridor downstairs to prevent overcrowding.
What the people were
protesting are the laws that will require landlords to pay an annual fee of
$150 per unit and a $250 penalty for each day the fee is not paid. They are
also agitated as ‘hot spots 911’ will force a fee for each response by police
that exceeds a pre-determined number.
One landlady stood up
and said, “Why are you putting all the landlords in the same boat? I don’t live
in a bad section of town, so I don’t understand why I’m being treated the same.
I feel targeted and insulted.”
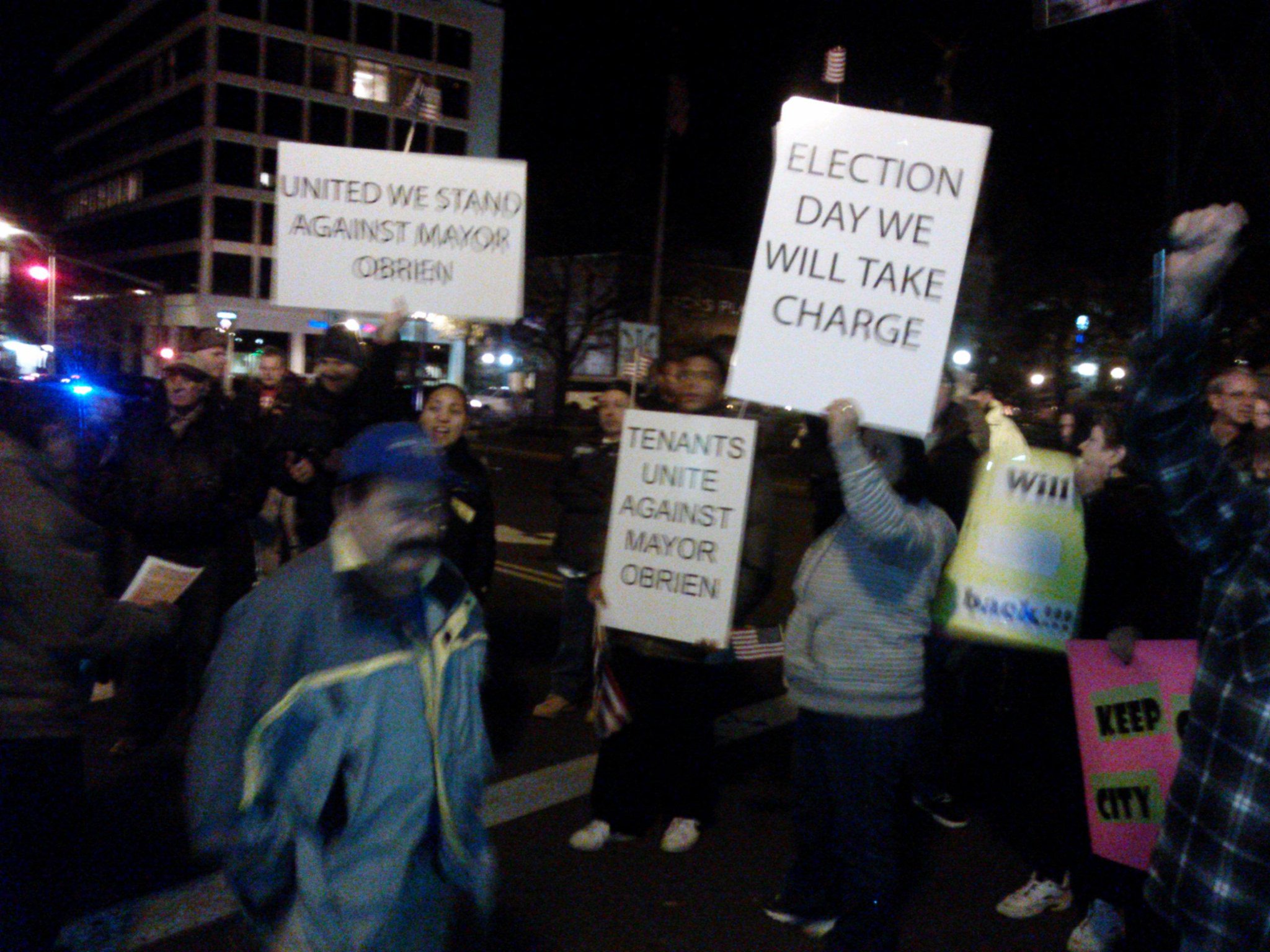
Many tenants were
complaining that they couldn’t afford the increase in rent as their
expendable income is
low enough as it is. Chants of, ‘The Shelter cannot take anymore’ were heard
outside of the city hall as billboards saying ‘Where will I go if I have to
move?’ were held aloft.
Landlord Sam Zurker
confronted Mayor O’Brian claiming that, “The slumlord of New Britain is the
city of New Britain. The Mayor is targeting one of two essential aspects of
life. The two are housing and food. He’s making it so that we cannot afford
food because the price of rent is going through the roof.”

Re-election for Mayor
is not until November 2013, but voters are already looking to go elsewhere as
they look forward to having the power to vote Tim O’Brian out of office.
Video Footage - http://a.yfrog.com/img526/6881/1zmxctadgzdeancbsgidle.mp4
Labels:
CCSU,
Clitheroe,
Connecticut,
Council Meeting,
Journalism,
Landlords,
Mayor O'Brian,
Media,
New Britain,
Police,
Protests,
Travel,
UCLan,
USA
Wednesday, 14 November 2012
Furniture Freak!
Despite my change in career I will always be attracted to articles of well made furniture. What people fail to notice is that a well designed, well made piece of furniture is no less a piece of art than a painting. Arguably more so, as there are more aspects to master and deliver to the consumer, but then again I'm biased. I would love to return to the trade at some point in my life, whether it be professionally or via a well kitted out garage/shed in my future home. Fingers crossed.
It is nice to hear that my former employer Paul Case is doing extremely well, and is moving onwards and upwards with his business. I'd like to share with you all a post on another blog 'Confessions of a Design Geek'
Website: www.confessionsofadesigngeek.com
Congratulations Paul on all your recent publicity and I hope that Paul Case Furniture continues to flourish. Just make sure you remember to keep the dust tray anally tidy!
For more info go to:
www.paulcase.co.uk
Twitter - pcasefurniture
Facebook - www.facebook.com/pages/Paul-Case-Furniture/123998710951542
It is nice to hear that my former employer Paul Case is doing extremely well, and is moving onwards and upwards with his business. I'd like to share with you all a post on another blog 'Confessions of a Design Geek'
Website: www.confessionsofadesigngeek.com
here’s one I made earlier :: paul case furniture
by DESIGN GEEK on Nov 14, 2012 • 8:30 amNo Comments
I met Paul Case at the Decorex exhibitors’ launch where I was speaking on behalf of Maggie’s, who was their charity partner this year. He has just launched his first range of furniture, having previously specialised in making one-off bespoke furniture for individual clients. I am delighted to be able to share with you the process of how it all happened.

When creating bespoke furniture, Paul was creating something new for every brief, making each item for the first time every time. Whilst very satisfying, it isn’t very economical, so he decided to create a range of furniture. The process worked in much the same way as for his bespoke work, except this time he was the client.
He started sketching and quickly came up with about 15 workable designs, but the sketch for the Sypder dining table above really stood out. Paul said: “It’s so simple to look at. The lines flow from one end to another. You run your finger along an edge and every line flows all the way through to the end of the table.” Having settled on the design, and sketched out some chairs to match, he set about calculating the angles that would be involved.

After many many pieces of paper like this one, he decided to “just make it and work it out.” He found that each angle was dictated by the piece it was being fixed to, so it was much easier to make a prototype and then take the angles from that.

This is that prototype and now Paul’s family dining table. What’s striking it how similar it looks to the original sketch. It had corner braces, because at this stage Paul had not fully worked out the joints. He took the prototype to the Celebration of Craftsmanship show in Cheltenham and got some good feedback from John Makepeace, Godfather of British furniture design, who later described it as “a form and structure that expresses the functional, structural and the visual role of a table”.

Once Paul was happy with the prototype (and had measured all those angles!) he was able to start making in his workshop. The first step is to prepare the timber and make the tapered shapes. Paul uses jigs for speed and consistency in getting the angles right.

The aesthetic is very much driven structural requirements. For example in the table, the structure can be very lightweight because the forces are channelled through the angled legs and balanced out in the stretcher. The rails under the table top form a ‘tie ring’ which works with the stretcher to give rigidity to the legs. Even the tapers in the legs are structural because the width of the leg reduces as the twist forces also reduce. The rails and the top surface are fully bonded together to give more stiffness which means that the top achieves a slender look considering the span it achieves.

Everything is finished by hand in this case by Paul… et voila!

Paul has also kindly allowed me to share this film with you, which documents the making process of one of his bespoke pieces of furniture. It’s absolutely beautiful and really demonstrates the craftsmanship that goes into everyone of this products.
Further reading for the especially geeky:
Tags: bespoke furniture, chairs, Decorex, dining chairs, dining table, furniture design, here's one I made earlier,Paul Case Furniture, Spyder collection
www.confessionsofadesigngeek.comCongratulations Paul on all your recent publicity and I hope that Paul Case Furniture continues to flourish. Just make sure you remember to keep the dust tray anally tidy!
For more info go to:
www.paulcase.co.uk
Twitter - pcasefurniture
Facebook - www.facebook.com/pages/Paul-Case-Furniture/123998710951542
Labels:
Bespoke Furniture,
Cabinet Making,
chairs,
Clitheroe,
confessions of a design geek,
Connecticut,
Decorex,
dining chairs,
dining table,
furniture design,
paul case furniture,
spyder collection,
Travel,
UCLan,
USA
Sunday, 11 November 2012
Thankyou!!!
It's just occurred to me that my blog has recently reached 1000 views. I'd like to thank all my readers for having a nosey and hope that it has provided interesting/entertaining reading. I know full well that Evan is one of my dedicated readers on Tuesdays and Thursdays during his 'Intro to Art History' lesson, at the back of the classroom on his phone. I'll keep this updated if only for you mate.
Keep coming back to get up to date on my battle with American Fat,my continuous search for banana milkshake, my Creative Writing drafts, and my adventures which have yet to include, Thanksgiving, New York, Florida, Christmas & New Year, Disney World (fingers crossed), and Texas to name a few.
Thanks again
Keep coming back to get up to date on my battle with American Fat,my continuous search for banana milkshake, my Creative Writing drafts, and my adventures which have yet to include, Thanksgiving, New York, Florida, Christmas & New Year, Disney World (fingers crossed), and Texas to name a few.
Thanks again
Monday, 5 November 2012
Storify
As part of my Journalism studies, we have to explore the impact of social media and the internet. During this period we have to use 'Storify' to publish our stories. Our first story was based upon either Hurricane Sandy or the postponement of Halloween. Here is my story:
http://storify.com/PhilNorth4/hurricane-sandy-is-down-to-homosexuals
As I write more, I will put the link somewhere on the blog
http://storify.com/PhilNorth4/hurricane-sandy-is-down-to-homosexuals
As I write more, I will put the link somewhere on the blog
Labels:
CCSU,
Clitheroe,
Connecticut,
Halloween,
Homosexual,
Hurricane Sandy,
John McTernan,
Rain,
Sandy,
Travel,
UCLan,
USA,
Wind
America Doesn't Know What It's Missing
After my long hard search for Strongbow, I finally managed to find it. I also managed to find some American Ciders in the pubs of Boston and have even converted the girls at Bentley University to cider. The next search is for Banana Milkshake. I didn't even realise that this would become a problem as I walked into McDonald's and asked for a super-size big mac meal with 'nana milkshake. I was corrected that they no longer do super-size. Gutted - this was one of the reasons I came here, to see for myself the true size of American food. Settling with a large (burger the same size, chips a bit bigger) I asked for a 'nana milkshake. Looking forward to my bucket of nectar, you could imagine my expression when I get a small red mixture. When I report that I asked for 'nana milkshake they said that they don't do banana milkshake and that a banana and strawberry smoothie was the closest. Disgruntled I leave to eat my small meal.
At first I thought this must be a one off, so a few days later I tried again at another McDonald's but once again was handed this crappy red smoothie. Game on, I needed to find a 'nana milkshake. Scouring the shops I found that there is only vanilla, strawberry, or chocolate - no banana. I was so happy when I found Banana Colada. My face was that of a child at Christmas but soon turned to the child who got socks when it tasted more of pineapples than banana; it was horrible.
I am having to settle for making my own in the canteen of real bananas, vanilla ice cream, and cream, but it's not really the same. Wish me luck in my search
P.S - In other news, I have converted Evan (coach) into eating Chip Butties. He now eats one most days after tea. Next I will introduce 'nana butties into this environment.
Bananas & Chocolate Milk
Due to the lack of football in my weekly schedule, mixed with 'all you can eat' canteen for the majority of the day, things are turning a little bit more rotund. The thought of pre-season training when I return to England is already haunting me. I hate the Castle steps, they kill me as it is, let alone if I'm carrying extra weight. Jake Chadwick will lap me twice rather than the standard once.
To try and combat this, Evan has taken up the role of Coach for Jon and I. Jon used to be a thin, speedy footballer. Now, however, due to injury has the build more similar to a Tighthead Prop. Coach used to run track all through high school and the beginning of University, but after multiple injuries to his knee and foot, has called it a day. After nearing 185lbs, his heaviest of all time, he decided to get back into running, regardless of it being competitive or not.
We started the 'trail run' through the park and woodlands on Saturday and got roughly 3 miles under our belts before having an hour or two break and hitting the gym. My dad and older sister will be so disgusted with me. However, during this run, Jon struggled immensely and left a trail of half digested pineapples along the route. 6 lots of breadcrumbs to be exact. Once in the gym, after making him sweat on the bike for 20 minutes, he was in his element showing Coach and I up on the weights as we struggled with the machines on the lower settings.
After having Sunday off for various reasons (non of which were alcohol related) Coach woke us both up at 6.45am for a Monday morning run. As Coach and I increased our stride, we found that we had left Jon. Jogging on the spot for five minutes for him to catch up, we still found no sign of our Prop. Changing our route to try and find him, we made our way back to the beginning and did a lap of the pond. As we neared the end we saw our bulky friend re-appear with tears and drool dripping from his face. He had taken a wrong turn and ended up making 7 lots of breadcrumbs.
Going straight for breakfast, Coach tells us to eat bananas and drink chocolate milk. The reason for this is potassium from the bananas for energy, and apparently the chocolate milk helps your muscles recover quickly. http://www.webmd.com/fitness-exercise/news/20100604/chocolate-milk-refuels-muscles-after-workout
To keep up to date on my weekly weigh-ins, go to 'To Be Fat Or Skinny'
Labels:
Bananas,
CCSU,
Chocolate Milk,
Clitheroe,
Connecticut,
Gym,
Running,
Travel,
UCLan,
USA
Saturday, 3 November 2012
Sandy, Halloween & Room Change
Hello everyone. Not only have I now survived an American style earthquake, but Hurricane Sandy. The funny thing is that when it first hit Cuba, my older sister was there on her first holiday abroad in many years. Luckily she is safe and sound only really having to spend one day inside, and is already looking to go back. Meanwhile up in America, hell let loose. Every time you turned on the TV, it was telling me the latest update on Sandy. When it would hit the east coast, where about it would hit, what time it would hit etc. CCSU cancelled all classes on Sunday for the Monday and Tuesday, roughly when it should hit New York. The canteen shut early and gave everyone a bag of food to take back to their dorms so that no one went hungry. After looking at the queue I decided to skip, preferring the idea of the Doritos Nacho Cheese crisps in the vending machine downstairs. Erik later reported that things got close to a riot with people fighting to get the free food, cutting the queue and arguing amongst each other. The funny thing was, New Britain avoided everything.
![]() |
Pretty Much Sums It Up |
Monday arrived and campus was dead. It was overcast with a wind that would pick up every now and then, nothing special, nothing different to a windy day back home. As the day progressed it began to rain, but again, nothing that different to home. The winds got stronger that would have people in England commenting on it. Meanwhile in New York, all public transportation was down, the subway flooded and a crane collapsed. That night Jon and I spent the night in the pub watching the occasional downpour out of the window.
Tuesday arrived and campus was fine, with the worst over we was surprised that CCSU had cancelled lessons so quickly. Realising that any chance of Wednesday being cancelled were well and truly out of the window, I sat down and rattled through the work that was due for the following day. Evan on the other hand, had the CCSU website on throughout the day waiting for confirmation one way or the other before starting anything. He got up a website that showed the state of Connecticut and the power outages. Apparently New Britain was the only part of Connecticut that has 0% power outage. All the towns and cities that surrounded us varied from 30% to 100% so I guess we were lucky.
Of course Halloween is huge over here in America, and with Halloween parties left, right, and centre, I guess I would have to dress up for the first time since I was 11 years old. Evan and I decided to have a gander down the Halloween shop (yes a shop dedicated to Halloween). What I noticed was that scary costumes aren't a necessity over here. Over the days I found on Facebook people back home dressing as Zombies, Monsters, Murderers etc. As we looked through the costumes, it was more like a fancy dress shop, with a small section for scary outfits in the corner. The stupid thing was the price of the decorations. For example a full sized werewolf that moved it's head left to right whilst roaring - $250. Halloween is huge here.
After wandering around for a while, nothing really leaped out at us with the decision being Sperm-Man and Grover. That's when we saw the women's section. I can't remember who first brought the idea forward, but the idea of dressing up as women was agreed to - worryingly with little resistance. After looking at the prices, we decided it would be cheaper to just nip to TK Max, this is where things got silly.
Eva & Phillipa |
Looking around TK Max we finally found the dresses in large that were cheap. Now how the hell are you meant to know if it fits or not without trying it on? Unlike a t-shirt which holds it's shape when you take it off, a dress doesn't. We ended up calling over the assistant who helped hold it against my back to see if my little red dress would at least leave something to the imagination. Once dresses were agreed to, it was then underwear. Again, no idea what size we are, we decide to try bras on over our t-shirts - apparently I'm a 40C (depending how many socks I use I guess). Then onto knickers in extra large that were a little too tight for comfort but would prevent any spillages should I lose my female mannerisms and sit with my legs slightly parted. With a pair of knee high socks added to the pile we looked at heels, but with size 13UK - 14US I didn't hold out hope.
![]() |
Sofia, Me, Evan, Erik |
A little reluctant to lower my head onto the cue like usual. |
The first party was on my birthday (28th Oct) and so I was supplied with a crate of Angry Orchard Cider from Jon, to go with the box of white wine Evan and I were sharing (ladies don't drink beer). Lets just say that it was my first wine/cider hangover and will be my last. The party that we got the outfits for was the one at Elmers with best dressed getting $100, $50, and $25 for 1st, 2nd, and 3rd. Our outfits went down extremely well with the barstaff in stitches and multiple slaps on the arse. The funniest however was when I sat on the pool table with Erik, a random guy asked me to turn around for his friend. Apparently his friend didn't believe I was a guy from behind. I've heard of beer goggles, but that's a little extreme. Evan and I tested our pool playing abilities in our dresses, trying to make sure not to flash. This proved a little difficult, especially when I had to lift a leg on the table for a long shot. Also, having boobs makes playing pool difficult as the cue moves out of line when you draw with your boob deflecting it off course.
As I said before, there were no scary costumes at either party. There was Spiderman, a Banana, Red Soda Cups, a Cheetah, Pirates, School Girls, a guy with ET in a basket with handlebars attached to his waist, American Football Referees, The Mask (Jim Carey), a Doctor etc. The scariest (if you could call it that) was a witch and a devil. Very strange. I have yet to hear as yet whether I have won or not yet, but I'm no longer holding up my hopes. Looks like I'm going to have to take my custom else where now.
I am now the proud tenant of a single room. My roommate has been evicted for breaking the rules too many times throughout his time here at the CCSU dormitories I had heard rumours that he was being evicted but he didn't say anything so I put them down to just that, rumours. I was then surprised to find all his things gone from the room when I came back from lessons. With it being too late in the semester to find someone else, I have a double room to myself until Christmas. Well, that was until Jon found out. Living 30-40 minutes away, he has often slept on the floor when he's had a few beers so as to not drink drive. Now with an empty bed in my dorm, he has moved in, albeit under the radar of officials. I don't mind, he's brought a big TV and his Xbox, so it looks like I'm going to get my fix of FIFA 13 after all.
Labels:
CCSU,
Clitheroe,
Connecticut,
Halloween,
Hurricane Sandy,
Rain,
Sandy,
Travel,
UCLan,
USA,
Weather,
Wind
Subscribe to:
Posts (Atom)